3D concrete printing poses opportunities for construction, design industries
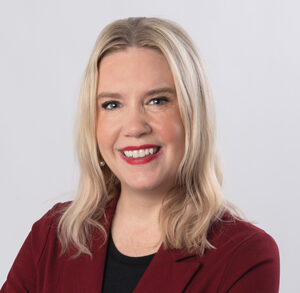
Lisa Rossi Jul 4, 2025 | 6:00 am
8 min read time
1,853 wordsBusiness Record Insider, Innovation and EntrepreneurshipIt’s messy. It’s not glamorous. And it’s not easy.
3D concrete printing is happening in Iowa and could become a revolutionary technology for the construction industry in the next 10 years.
One hub of research and practice is at Iowa State University. Since about 2022, the university has worked to develop 3D printing research and methods to teach 3D printing through multiple efforts, said Shelby Doyle, associate professor of architecture and Stan G. Thurston professor in design build.
“My role in that was to figure out how do you teach design students how to 3D print and how to 3D print concrete,” Doyle said. “And then to develop that setup at Iowa State — develop the equipment and the software and the hardware, and how do you mix the material and how do you teach someone how to do that?”
The university purchased a ceramic 3D printer capable of printing large-scale clay and cement objects, which was paid for with part of an approximately $2 million Iowa Economic Development Authority grant for Iowa State’s 3D Affordable Innovative Technologies Housing Project.
The team recently found an industry partnership in which they could learn and teach about 3D concrete printing and support an Iowa community after a tornado.
Doyle and ISU partnered with Midwest-based design firm OPN Architects last summer to create a 3D-printed seating installation outside the new library in Rudd, after the previous building was destroyed by a tornado in December 2021.
“OPN is really interested in pursuing these emerging technologies and how we can put them into our workflows,” said Jacob Gasper, architectural designer at OPN. “This was a great opportunity for us to get involved in current research that’s going on at Iowa State, but also bring OPN’s workflows and our expertise and our knowledge and help the university as well.”
The outdoor seating space, shaped in figure eights, featured seven different 3D printed concrete pieces that allows patrons to sit or recline on them.
“Usually in an architectural project, you make drawings, and then people build from the drawings,” Doyle said. “And as we do more 3D models, there’s a lot of interest in how do you go straight from model to construction?”
She said the team used augmented reality to visualize the formation of the different pieces before printing them. Now the ISU team can look at using AR for future projects.
Jamie Craine, an architectural designer with OPN, said experience with augmented reality was something the firm brought to the partnership.
“That’s something we feel really confident in our skills,” Craine said. “We have used them with contractors as well to visualize exactly where something will be located on the building site. … So that was something that we wanted to work through that process on this project as well. We used it to fabricate the reinforcement – the steel. We also used it on site to install the objects as well.”
Lessons learned
Gasper said 3D printing is “very laborious.”
“3D printing also is not just like pushing a button and letting it magically go,” he said.
The way it works, Gasper said, is someone mixes the concrete in a mixer and then it is transferred into a machine that pumps it and vibrates it to get the air out. Then, it’s pumped through a hose and then it gets deposited, he said.
“Somebody has to be mixing the concrete. Somebody has to be making sure the hose isn’t clogging or getting too hot. Somebody has to be watching the print because sometimes there are air bubbles that create holes in the print,” he said. “Like, are robots going to take our jobs? I just think they’re going to do specific things that they’re maybe better at than we are, but we are still programming them. We‘re still working with them to make sure they’re printing correctly, cleaning them up.”
“It’s not exactly glamorous,” Craine said. “Hopefully in the future it will be a little bit more refined.”
Craine said the team also had to figure out how to transport the heavy pieces from ISU to the library in Rudd.
The team used a pallet jack to lift the 250 to 300 pound objects off the pallets and then they used a furniture dolly, Craine said.
“Three of us would lift each object on with the dolly and I rolled it into a U-Haul and then rolled it back out,” she said. “I think there were probably better ways to do that.”
Gasper said the objects were “medium scale,” meaning they didn’t need a crane, but they were also too heavy to pick up.
“A lot of 3D printing is done on site versus prefabricated and moved,” Craine said. “So this was a unique case where we did have to move them, store them, process them again. … It was just a new endeavor, that every step of the way we were problem-solving and strategizing.”
Doyle said there is sometimes “a real misunderstanding” of how much labor goes into 3D printing.
“You don’t just push ‘print,’” she said. “And I think that’s usually why it’s like, ‘Oh, we can print buildings so they’ll take two hours or something,’ and I think that really does a disservice to how much knowledge it takes to build well.”
Working with the 3D printer has made her realize how much human ingenuity exists, she said.
“So much of the project is about communicating and building off of existing knowledge, rather than replacing it,” she said.
Others in Iowa have also embarked on the journey of 3D concrete printing.
Zachary Mannheimer is board chair and founder of Alquist 3D, a company he started at the end of 2020 that does 3D concrete printing. He’s based in Iowa City and the company headquarters is in Greeley, Colo.
Alquist 3D was involved in the project to build the first 3D-printed home in Iowa — in Muscatine — but it had to be torn down because “the concrete formula that met the necessary requirements in lab testing did not meet the same requirements while on site,” reported WQAD.
The Community Foundation of Greater Muscatine was overseeing the project, and had been working with Alquist 3D, reported the Des Moines Register.
Mannheimer said of the project, “The two parties disagreed and Alquist decided to move on after the community.”
“So there’s been a lot of ups and downs with the company since we started,” he said in an interview. “Today we’re at about 22 employees. We’ve grown significantly. We’ve taken on a lot more projects.”
One of those projects is an 8,000-square-foot addition to a Walmart in Athens, Tenn. It is one of the tallest 3D concrete-printed structures in the world, according to the company.
The company had never printed anything that large or high in such a short period of time, Mannheimer said.
“It was a great challenge for us as a company and for us as an industry,” he said. “We learned how to go quicker and [at a] lower cost. Because of these projects, now we’re taking what we learned and going back to the residential sector later this year.”
The future of 3D concrete printing
3D concrete printing presents many opportunities for new approaches to design as well as construction.
Doyle said one benefit of using a 3D printer is “geometric freedom.”
“You can print things that would be very expensive to buy a mold for,” she said.
Another hope for 3D printing is that it would use less material, because you would only put in the material that you need, she said.
“And then there’s ideas that [it] might reduce labor, but I think it’ll really just be different types of labor,” Doyle said. “I think you still need all of the people to run the machines and do the software and do the mixing and finish and install after.
“So it doesn’t necessarily eliminate jobs so much as create different types of jobs.”
Craine said the method also allows for more creative freedom.
“I think you can do a lot of really unique forms that can impact environments and things like that that maybe you couldn’t do with traditional methods,” she said.
Also, during design, it’s a lot more nimble, she said.
For example, the team faced some safety concerns during the project, so they had to adjust the sizing to make sure kids couldn’t get their heads stuck in the 3D printed concrete pieces, a concern they hadn’t thought of in the beginning, Craine said.
“We can make small adjustments as we go really easily when we set up those parameters and then modify as we learn more about the project and more about what’s needed,” she said.
Mannheimer said he predicts the technology will revolutionize the industry in the next 10 years.
“What I’ve learned about 3D printing is it’s an incredible technology that within the next 10 years is likely going to be on every job site in America,” he said. “That’s where the industry is going. … What I also learned is back when I first heard about 3D [printing] in 2016, it was marketed as the end-all, be-all solution for affordable housing and other construction methods and was going to lower costs dramatically. Turned out that’s not necessarily true, and the industry is still pushing to get costs to come down below traditional housing costs.”
Dana Sorensen, associate principal at BNIM, a design company with locations in Kansas City and Des Moines, said he was part of a group that collaborated with Iowa State in Hamburg to build a 3D-printed home that never came to fruition.
He said it wasn’t 3D printing problems that derailed the project but issues with the developer.
“I think [the] technology has a long ways to go, both in terms of how it’s used in our climate specifically, but also in the scale of projects that can be used,” he said. “I think there’s a lot of promise in it.”
He said how and where it’s used will be important. He said he could see its place in utilitarian buildings and places “where we have to rapidly deploy buildings, such as disaster response areas.”
Doyle said she’s interested in material development and wants to see if “we can find a way to make a super local material.”
“We’ve been working with ground up wind turbine blades and corn stover ash to create a more locally sourced material,” she said.
Innovation, she said, happens in increments.
“You’re building upon things that came before you, and a lot of this is just a willingness to try,” she said. “So much of research is a willingness to risk something that you don’t know how it’ll turn out.”
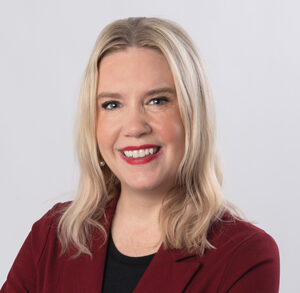
Lisa Rossi
Lisa Rossi is a staff writer at Business Record. She covers innovation and entrepreneurship, insurance, health care, and Iowa Stops Hunger.